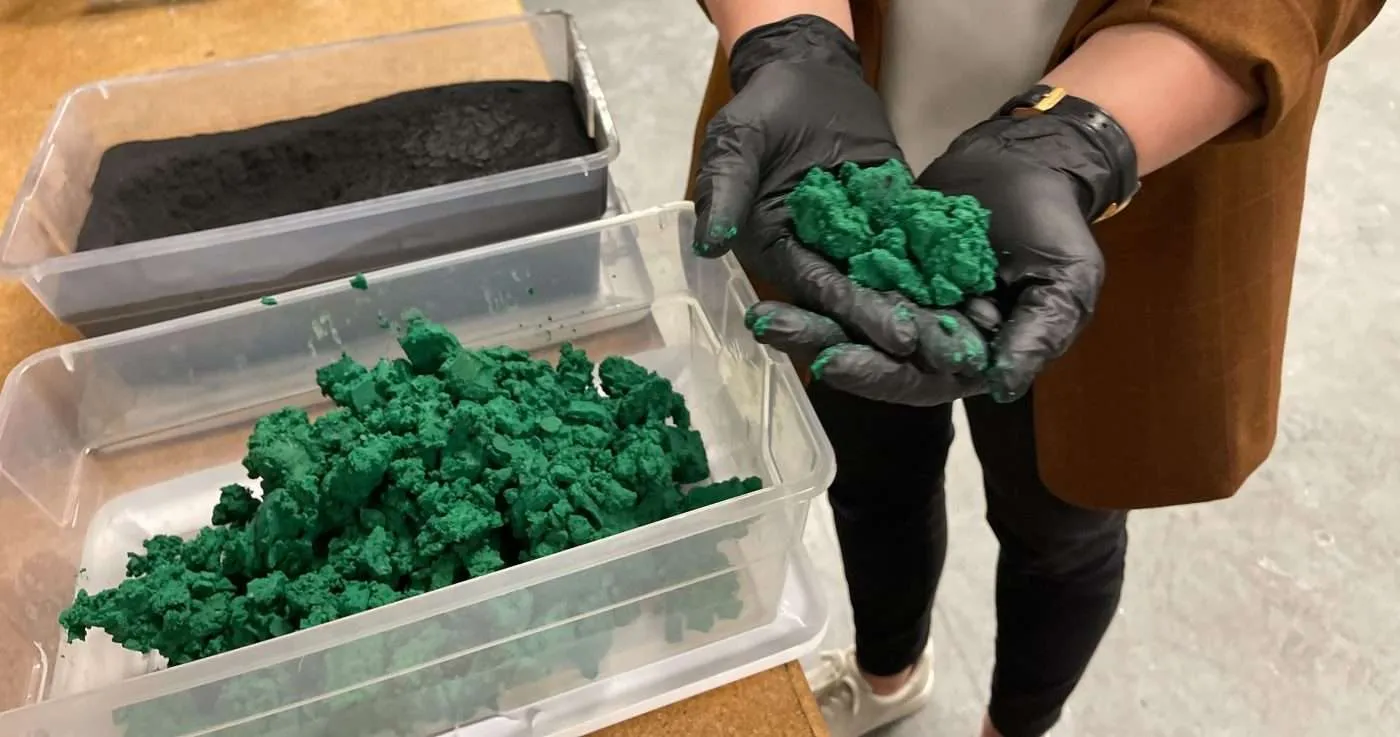
LEADERS IN SUSTAINABLE METAL REFINING
Notice: Undefined index: options in /home/xs999583/sustainaseed.net/public_html/db.sustainaseed.net/wp-content/themes/dlist/inc/directorist-support.php on line 318
Notice: Trying to access array offset on value of type null in /home/xs999583/sustainaseed.net/public_html/db.sustainaseed.net/wp-content/themes/dlist/inc/directorist-support.php on line 318
Notice: Trying to access array offset on value of type null in /home/xs999583/sustainaseed.net/public_html/db.sustainaseed.net/wp-content/themes/dlist/inc/directorist-support.php on line 318
What we do
We are revolutionizing metal refining with our safe, low-emission technology to create a sustainable foundation for the electrified economy. Our mission: to keep critical metals in circulation forever with the lowest impact on the environment.
A Cleaner Metal Refining Technology
Imagine being able to refine metals cleanly and safely on site, creating an endless supply of products, using just the raw materials you have on hand. Meet the Oyster, its core technology is the future of metal refining, found in a 2000-square foot modular unit. Its small footprint makes it ideal to install onsite even in the most remote locations, and its flexible design fits your production needs. By creating a circular loop, there’s no need to ship raw materials for processing.
Modernizing Refining through Electro-Extraction
Electrochemistry is at the heart of The Oyster — our modular refining unit that fully replaces traditional smelting. We designed this system through combining electrochemistry, chemical precipitation, and filtration to process metal-bearing feedstock material in the most efficient and selective way. Nth Cycle’s unique electro-extraction process can tune two parameters at the same time — both the electrical current and pH, which allows us to target and recover a specific metal or groups of metals, producing metal and metal salts for resale.
Company's story
A sustainable future requires a sustainable method to refine metals. The Oyster, our patented modular refining system, extracts high-purity critical metals of any type, in any state, using just electricity and water. Our clean and less-energy intensive electro-extraction technology is the modern answer to the antiquated, energy-intensive smelting of the past. We’re fixing the broken global refining supply chain by locating our scalable modular units onsite, right where the feedstock is.
We’re meeting the immediate need for critical metals to power the clean-energy transition. We’ve created a circular refining method to consistently deliver pure, critical metals that the world demands now. The Oyster, our patented modular unit, can be installed anywhere. Designed to scale, the Oyster accommodates a client’s production and is operational in mere months, not years. The swift set-up time reduces carbon emissions once spent on shipping metals across the globe for processing.
Our passion is to transform the metals-refining industry for a modern economy. An executive team of industry experts, with over 150 years of combined experience, are led by CEO Megan O’Connor, PhD, along with co-founders Desiree Plata, PhD, and Chad Vecitis, PhD, developed an advanced electro-extraction technology to safely produce the critical metals needed for an electrified economy. We are passionate that our technology can forge a proper circular economy.
The Oyster uses electro-extraction, combining water and electricity to recover critical metals. Electro-extraction is a safer and less energy-intensive alternative to traditional, energy-intensive refining methods. Our novel, low-emission technology can be applied in mining, from extracting metal trapped within low-grade minerals and mining waste streams, to recycling, by salvaging material from end-of-life scrap. We’re closing the mining production loop and making metals infinitely reusable.
We partner with clients to understand their refining needs, deploying our modular and scalable Oyster extraction units on site, saving clients time, capital, and the carbon emissions associated with transporting material to traditional refining and recycling facilities.
General Information
Gallery
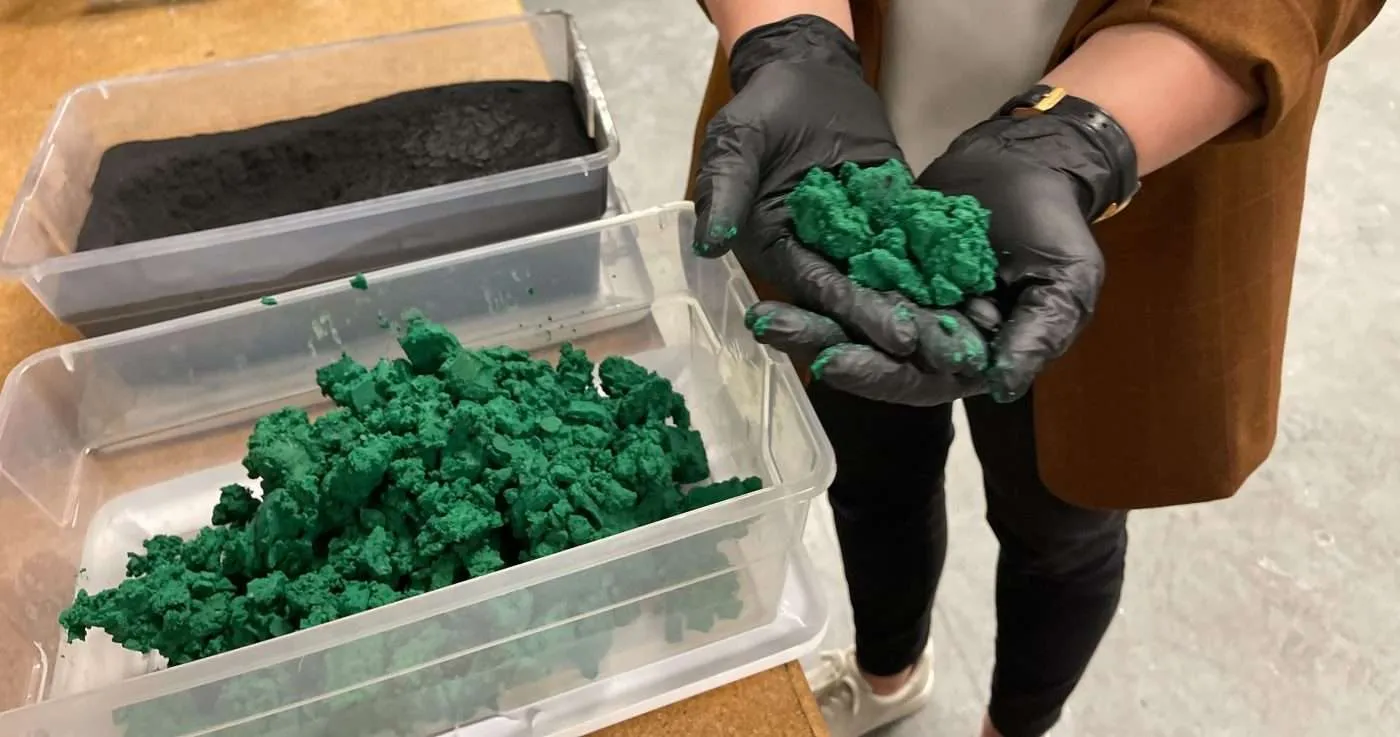