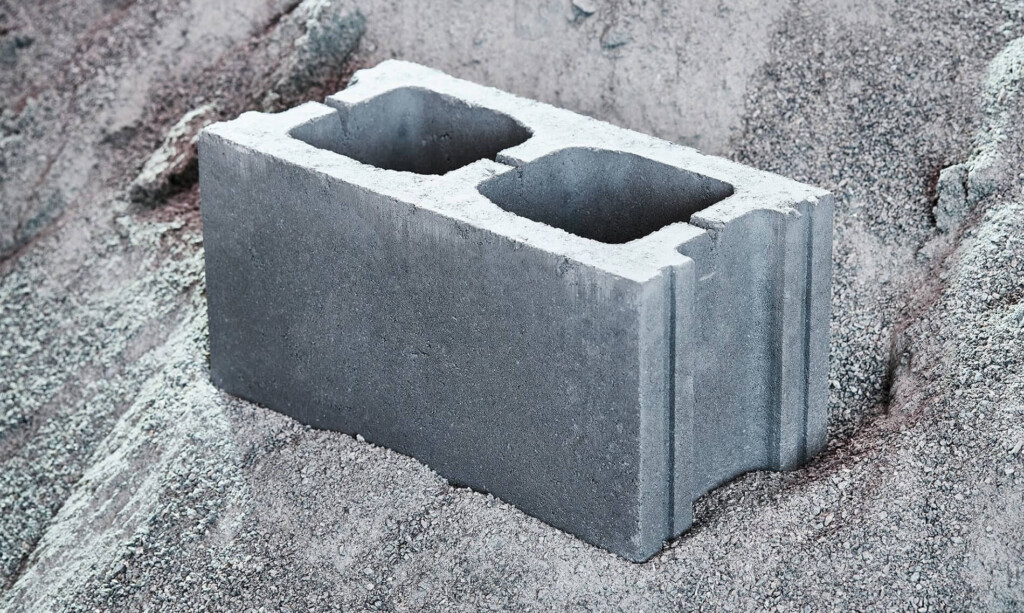
Concrete carbon removal
Notice: Undefined index: options in /home/xs999583/sustainaseed.net/public_html/db.sustainaseed.net/wp-content/themes/dlist/inc/directorist-support.php on line 318
Notice: Trying to access array offset on value of type null in /home/xs999583/sustainaseed.net/public_html/db.sustainaseed.net/wp-content/themes/dlist/inc/directorist-support.php on line 318
Notice: Trying to access array offset on value of type null in /home/xs999583/sustainaseed.net/public_html/db.sustainaseed.net/wp-content/themes/dlist/inc/directorist-support.php on line 318
What we do
CarbiCrete offers precast concrete manufacturers the process, materials, and support to produce high-quality masonry and hardscape products in their existing plant at a lower cost, and in a way that reduces their embodied carbon.
Our technology enables the production of cement-free concrete using industrial by-products and captured CO2.
Company's story
Our Specialty
CO2 Curing
Our patented curing process involves the injection of CO2 into a curing chamber where it reacts with the steel slag within the fresh concrete. During the carbonation process, the CO2 is permanently captured and converted into stable calcium carbonates, filling the voids of the matrix to form a dense structure and giving the concrete its strength.
Concrete Properties
When compared with cement-based CMUs, CarbiCrete CMUs exhibit equivalent or better mechanical and durability properties. They have the same water absorption properties, but higher compressive strength by up to 30% and display better freeze/thaw resistance. CarbiCrete CMUs meet or exceed ASTM C90 performance requirements.
Lifecycle Assessment
CarbiCrete’s net carbon-negative impact has been validated by a third-party verifier. It starts with a 100% reduction of carbon dioxide emissions associated with cement production. It drives net negative emissions with the permanent sequestration of carbon dioxide that is mineralized in the product during curing. Even when additional transportation and conversion impacts are considered, CarbiCrete’s full LCA results in net carbon-negative concrete products.
Our patented curing process involves the injection of CO2 into a curing chamber where it reacts with the steel slag within the fresh concrete. During the carbonation process, the CO2 is permanently captured and converted into stable calcium carbonates, filling the voids of the matrix to form a dense structure and giving the concrete its strength.
Concrete Properties
When compared with cement-based CMUs, CarbiCrete CMUs exhibit equivalent or better mechanical and durability properties. They have the same water absorption properties, but higher compressive strength by up to 30% and display better freeze/thaw resistance. CarbiCrete CMUs meet or exceed ASTM C90 performance requirements.
Lifecycle Assessment
CarbiCrete’s net carbon-negative impact has been validated by a third-party verifier. It starts with a 100% reduction of carbon dioxide emissions associated with cement production. It drives net negative emissions with the permanent sequestration of carbon dioxide that is mineralized in the product during curing. Even when additional transportation and conversion impacts are considered, CarbiCrete’s full LCA results in net carbon-negative concrete products.
Our story
The company’s patented technology was first developed at McGill University by Mehrdad Mahoutian, now CarbiCrete’s CTO, during his PhD studies under professor Yixin Shao.
Mahoutian was trying to find a by-product or waste material that would react with CO2 in a way that would enable the production of construction products that sequester carbon dioxide.
After testing a variety of materials, he found that steel slag, a steel-making by-product, could be used as a one-to-one replacement for cement when ground to the correct consistency.
In 2015, through the Technology Transfer Office at McGill, Mahoutian was introduced to Chris Stern, a cleantech entrepreneur that was looking for promising green technologies.
The pair teamed up with Yuri Mytko, a marketing professional, and Mario Venditti, a mechanical engineer and technology investor, and incorporated under the name CarbiCrete.
As its first project, the start-up elected to compete in the Carbon XPRIZE, a $20 million international competition challenging the world to develop valuable uses for CO2. The group was selected as a finalist in 2018.
During the four-year competition, the company attracted funding from a number of sources, including Innovobot, Venditti’s venture capital firm, and Harsco, the world’s largest processor of steel slag, and embarked on a multi-year pilot project to demonstrate that the technology was viable at industrial scale.
CarbiCrete identified Patio Drummond, a hardscape manufacturer in Drummondville, Quebec, as its pilot partner.
In 2022, CarbiCrete closed out a successful Series A funding round, bringing in a host of new investors, including FS Investors, Arc Energy Fund 9, Something Good Ventures, New Climate Ventures, MacKinnon, Bennett & Co., Fonds économie circulaire, Fonds de Solidarité FTQ, Fondaction, Aera VC, and French manufacturing giant Saint-Gobain, with whom CarbiCrete is working to bring the technology to France.
The company rounded out its management team and grew its staff to over 50 employees. After the successful completion of its pilot project, it was announced in September of 2023 that CarbiCrete products were now available on the market through Patio Drummond.
As CarbiCrete expands its global presence, the company is working with a number of partners to develop new cement-free products and to convert concrete plants to the CarbiCrete process.
CarbiCrete’s corporate headquarters and R&D facility are located in Lachine, Quebec.
Mahoutian was trying to find a by-product or waste material that would react with CO2 in a way that would enable the production of construction products that sequester carbon dioxide.
After testing a variety of materials, he found that steel slag, a steel-making by-product, could be used as a one-to-one replacement for cement when ground to the correct consistency.
In 2015, through the Technology Transfer Office at McGill, Mahoutian was introduced to Chris Stern, a cleantech entrepreneur that was looking for promising green technologies.
The pair teamed up with Yuri Mytko, a marketing professional, and Mario Venditti, a mechanical engineer and technology investor, and incorporated under the name CarbiCrete.
As its first project, the start-up elected to compete in the Carbon XPRIZE, a $20 million international competition challenging the world to develop valuable uses for CO2. The group was selected as a finalist in 2018.
During the four-year competition, the company attracted funding from a number of sources, including Innovobot, Venditti’s venture capital firm, and Harsco, the world’s largest processor of steel slag, and embarked on a multi-year pilot project to demonstrate that the technology was viable at industrial scale.
CarbiCrete identified Patio Drummond, a hardscape manufacturer in Drummondville, Quebec, as its pilot partner.
In 2022, CarbiCrete closed out a successful Series A funding round, bringing in a host of new investors, including FS Investors, Arc Energy Fund 9, Something Good Ventures, New Climate Ventures, MacKinnon, Bennett & Co., Fonds économie circulaire, Fonds de Solidarité FTQ, Fondaction, Aera VC, and French manufacturing giant Saint-Gobain, with whom CarbiCrete is working to bring the technology to France.
The company rounded out its management team and grew its staff to over 50 employees. After the successful completion of its pilot project, it was announced in September of 2023 that CarbiCrete products were now available on the market through Patio Drummond.
As CarbiCrete expands its global presence, the company is working with a number of partners to develop new cement-free products and to convert concrete plants to the CarbiCrete process.
CarbiCrete’s corporate headquarters and R&D facility are located in Lachine, Quebec.
General Information
Gallery
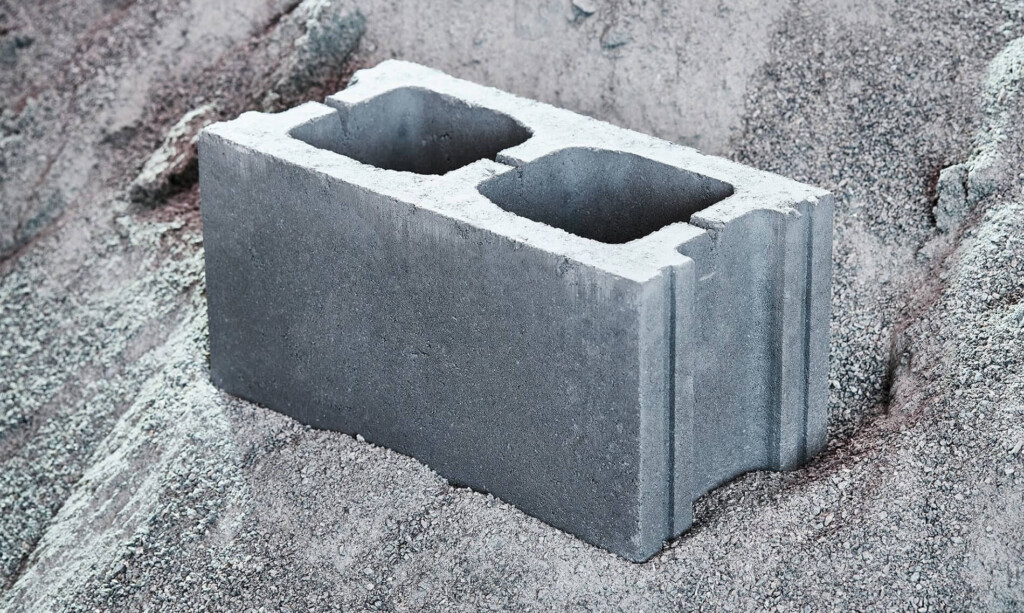