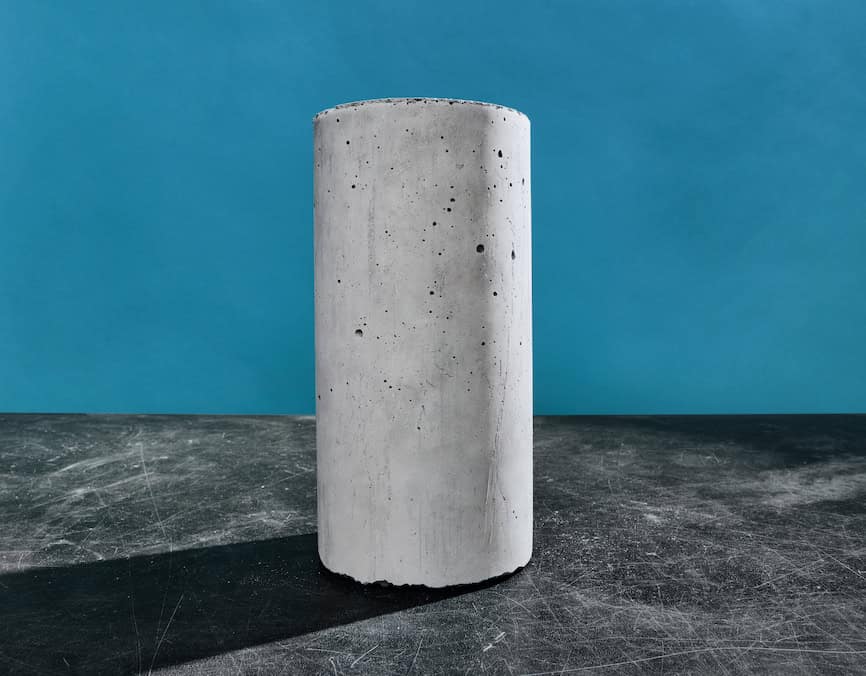
Low-carbon cement, so we can keep building.
Notice: Undefined index: options in /home/xs999583/sustainaseed.net/public_html/db.sustainaseed.net/wp-content/themes/dlist/inc/directorist-support.php on line 318
Notice: Trying to access array offset on value of type null in /home/xs999583/sustainaseed.net/public_html/db.sustainaseed.net/wp-content/themes/dlist/inc/directorist-support.php on line 318
Notice: Trying to access array offset on value of type null in /home/xs999583/sustainaseed.net/public_html/db.sustainaseed.net/wp-content/themes/dlist/inc/directorist-support.php on line 318
What we do
Our process makes the same concrete without the emissions
Today’s portland cement is made by cooking limestone, sand, and clay in massive fossil-fueled 1450°C kilns. This results in a tremendous amount of CO₂: on average 0.9 tonnes per tonne of OPC in the USA. About half of this CO₂ is released from limestone, which is ~50% by weight CO₂, as it decomposes in the kiln to form reactive lime. The other half of the CO₂ emissions is from the fossil fuel (often bituminous coal) needed to reach 1450°C, the temperature required to form the crystal structure characteristic of OPC. This temperature is currently impossible to electrify efficiently.
We skip both emissions sources, instead using the elegance of electrochemistry to extract reactive calcium (Sublime Lime™) and silicates from abundant raw materials that are then blended into a final Sublime Cement™. Our cement’s crystal structure is different than the OPC produced in a fiery kiln, but its performance and hardened phase in concrete are the same.
Company's story
We call our process true-zero
Our process decarbonizes cement production by avoiding CO₂ emissions in the first place. We skip the carbon addition and subtraction typical of net-zero solutions — and the associated expense and complexity of carbon capture, sequestration, credits, and clean up.
A refinery for rocks
Our process transforms electrical energy into chemical energy to break feedstocks down into their constituent elements. We then reassemble these pure, reactive ingredients into the ideal cement composition. We use every part of the rock, leading to near-zero waste, unlike the limestone mined for OPC, 50% of which ends up as greenhouse gas emissions or otherwise wasted.
The greatest CO₂ reduction impact from a green electron
Sublime was invented because the proliferation of renewable energy meant that the fossil-fueled processes of the Industrial Revolution could finally be electrified. While many decarbonization technologies are working to access this clean grid electricity, Sublime’s manufacturing has the highest impact. Each kWh displaces limestone emissions (the majority emissions from traditional cement-making) and the energy emissions from coal-fired kilns.
General Information
Gallery
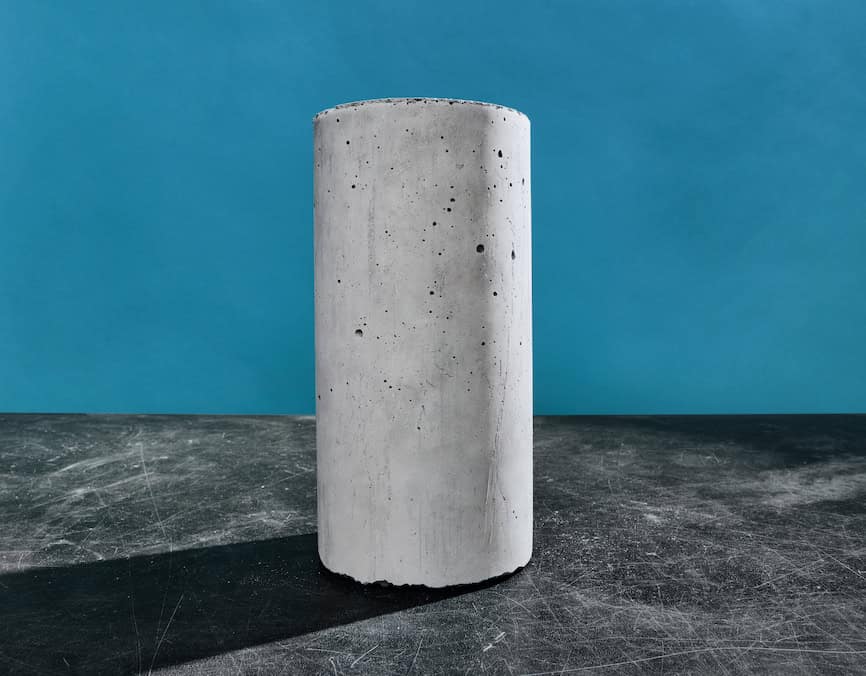